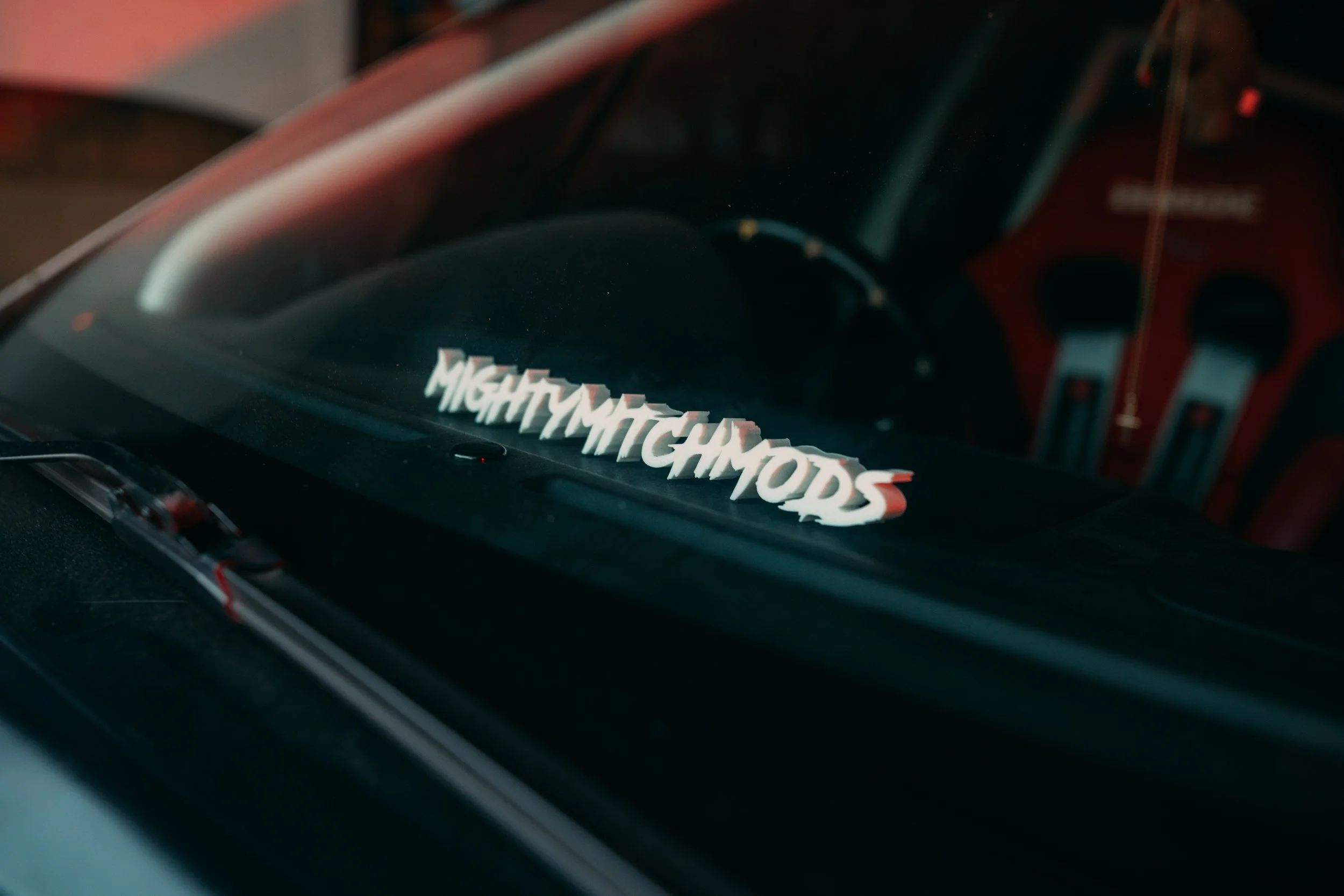
“My name is Mitch Ceko.
I’m a car enthusiast with a passion for custom fabrication. I’m a boiler maker by trade and i really enjoy when I get the opportunity to make custom parts for my car.
My car is a 2006 Subaru Impreza Wagon, which started its life as a n/a car. the car itself has been an ongoing project pretty much since when I first bought it. when it was first purchased, it was a completely stock Impreza. Now, it has nearly all the parts swapped out, modified or customised, or replaced with upgraded parts. I couldn’t be happier with how the car is coming along, it’s almost finished this next big stage of upgrades with a new engine and it’s very exciting to see the end is near. Soon, i’ll be driving it.”
How did the car start off & what is it now?
The car was a completely stock Impreza wagon luxury, which had the leather seats and sunroof. The choice of this car originally was not mine. For a while I didn’t have a car when I was 18 as I had an accident in my previous car. My mum is the one who found the car in car sales and asked if i wanted to go take a look at it. First thing i looked at was how much power it made, when I read it made a staggering 92kw at the engine, I said not a chance I don’t want the car. About a week later I decided that we would go take a look at it because it had a sunroof. Sure enough when I went and looked at the car and drove it, I loved it and drive home with it that day.
That’s where the car was, now it’s a wide body Impreza wagon with a whole list of upgraded and custom parts including airbag suspension, a high end sound system, full roll cage, heated bride bucket seats with 6 point harnesses, sti 6 speed gearbox and r180 diff, some fat 18x11 wheels with some meaty 295 semi slicks, and the most exciting part, the new engine. it’s a destroked ej25, making it a 2.3L, with a garrett g30-900 turbo, process west intake manifold and a whole list of custom parts in the engine bay.
Can you go into detail on what you’ve done, take us through the start to ‘almost’ finish process + all the little projects you’ve had with it & the custom work you’ve done?
The car from beginning to now has been a long process. I got the car in 2014, and along the way it’s had a few changes of wheels and suspension, but to go through the process on everything that’s now currently on the car is a long list, but i’ll do my best to mention as much as i can.
Let’s start with the body work, the metal flares and bonnet and wheel tubs. The metal flares i purchased from a company called ulterior motive, and they make the flares to your specs and design. the process of installing them was definitely not straight forward, as the one piece metal flare had to be welded to the guards, trim away all the excess material underneath, seal up everything to prevent rust, cut to allow the flare to go from the bumper to the guard and the hardest part was the rear flares where they go over the door. that area was difficult as you had to cut the door line through the flare and then fill in all the pieces underneath. it was a long process of fine welding and shaping sheet metal, then learning how to use body filler and paint. It was a big learning process doing all the body work and I enjoyed it, but i’m glad it’s done now. The bonnet wasn’t overly difficult after having learned what I did from doing the flares. The hardest part with it was marking out the bonnet as to where the vents would go. Lots of curved surfaces and body lines to try and work with, and have a functional vented bonnet to remove engine bay heat. and the wheel tubs in the engine bay were fun to do, as i got to get rid of a lot of the stock metal and weld in new flat and nice metal. The wheel tubs themselves are actually a trailer mud guard cut in half, and then sheeted in all around.
Next few things to talk about are some of the things i’ve made for the car. The roll cage to start with, it’s a full bolt in roll cage with nice interlocking joiners. I actually built a bender to bend up the roll cage, but purchased the dies for the pipe. It was another fun learning process as up until then, I had never really done any tube bending or much pipe work with intersecting joins, but all I needed was the bender and the pipe notching tool I have. I’ve also fabricated myself some front lower camber adjustable control arms as they currently don’t exist for purchase. It was another fun learning process making these, I made a jig from an alloy sti control to make sure i had all the geometry correct, and then it was cutting, bending and welding. some of the parts that i’ve made have had to had a lot more design work go in with some trial and error to get things right. Mainly 2 pieces, my alternator bracket and the twin calliper mount for the rear hubs. i used fusion 360 to 3d draw up some designs, and used my 3d printer to test pieces if they fit and work. The alternator relocation bracket was needed as I have a forward facing manifold, which means I have to get rid of either my alternator, which i can’t, a/c which I really didn’t want to, or power steering. so I decided to get rid of the stock power steering pump and then the alternator needed to go in its place. The little bracket that is hidden under the alternator is I believe version 4 or 5, which is a billet aluminium piece and to keep power steering I now have an electric power steering pump from a golden astra. The twin calliper rear hub mounting plate was another long process of design, test print, fit and then fix problems. and then lastly I got the pieces cnc plasma cut and welded them together.
Last big thing to talk about is the engine swap. Gone from a n/a 2L to a turbocharged 2.3L destroked ej25. It has a garrett g30-900 turbo with a 0.83 rear housing and turbosmart 50mm external wastegate. Will be running on flex fuel, so in case I can’t get e85 and I'm stuck I can use 98. Mounting the engine in was nice and simple, but from there all the custom fab started. I made the exhaust manifold and up pipe, dump pipe and the full exhaust. the catch cans, surge tank, radiator top tank, coolant overflow tank, window washer water tank, all the intercooler piping with interlocking clamps. then all the engine plumbing. I’ve tried to use braided lines and a/n fittings for everything on the engine bay to keep it looking pretty. the last cool thing I made that is in the engine bay is my strut brace, which hides the strut tops and also braces to the firewall. it’s mostly a showpiece, but it helps a little i guess.
Any reason as to why you went into an N/A instead of starting from a wrx?
At the time when I was looking for a car and I was on my p’s, it wasn’t legal to drive a wrx. and I really didn’t wanna risk my licence driving a turbo car that wasn’t allowed to everywhere.
Did you jump into this build mostly clueless on what to do? How did you teach yourself/get taught?
Growing up i’ve always been handy with tools and working on things, but never really touched cars. So when i got it yeah i’d say i didn’t really have all too much of an idea on what to do. In the beginning i was paying places to install parts and after seeing what they done and how simple looked I started to do more and more myself. I started with simpler projects and slowly learnt how things come apart and go back together. Youtube was also a very big help with a lot of things. I picked up a few skills like wiring, and I really found that with cars, as long as you label where stuff goes so you know how it all goes back together, it’s not too hard. Now with a car the only things i’m not confident with is engine or gearbox rebuilds. Apart from that, with my car now I know in my head almost perfectly every nut and bolt of how everything goes together and comes apart.
